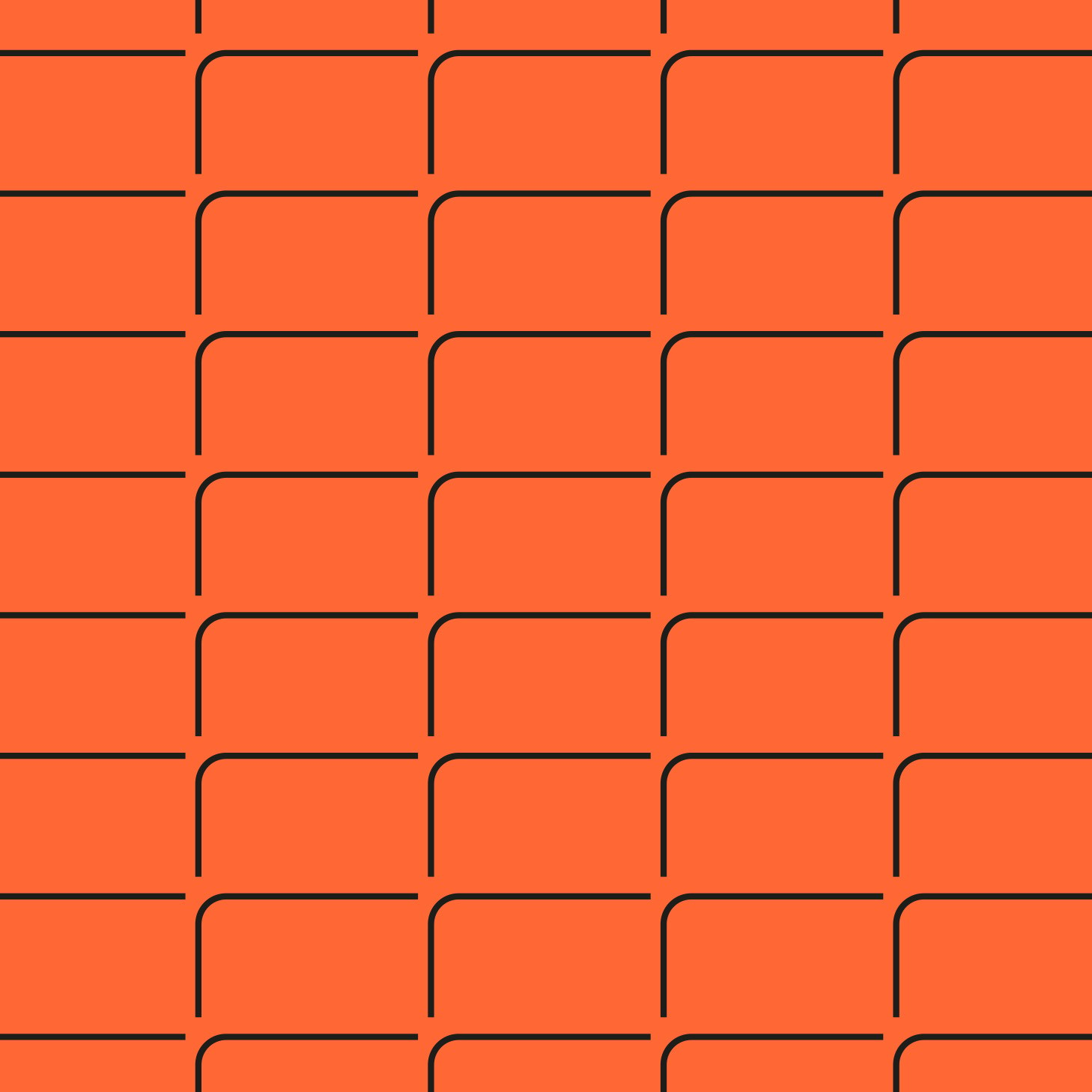
As EPCM contract structures gain popularity in global projects, related disputes will become increasingly complex. Key areas of contention will likely include costs recovery and delay provisions, as well as difficulties posed by a more complex allocation of liability inherent in EPCM structures.
By Erin Miller Rankin, Matei Purice and Robert Colvin
The global construction industry faces rising material costs, increasing project complexity from untested energy transition technologies, supply chain disruption and a persistent shortage of skilled labor. These challenges have cooled contractors’ risk appetite and prompted project owners to rethink their strategies for project delivery.
Contractors and owners alike are moving away from the traditional lump sum Engineering, Procurement and Construction (EPC) model in favour of EPCM (or Engineering, Procurement and Construction Management). This shift is driven by EPCM’s distinct risk profile for contractors and its perceived lower costs for project owners. The introduction of IChemE’s “Blue Book” in 2023, the first standard form EPCM contract, underscores this trend. While it remains the only standard form EPCM contract to date, FIDIC is expected to release its own version.
EPC contracts, sometimes referred to as “turnkey” contracts, have long been prevalent in privately funded major projects and publicly funded infrastructure developments. EPC contractors are tasked with delivering a completed asset to the project owner, meeting guaranteed performance standards by a fixed date and cost.
Under an EPC contract, the contractor assumes responsibility for all project elements – Engineering, Procurement, and Construction – along with the associated completion and performance risks. Typically, the project owner (or employer) is responsible for the specification of the facility, providing the site, making payments, and addressing delays it causes to the contractor. The contractor assumes responsibility for all other aspects, subject to a specified liability cap.
In contrast, EPCM contracts are (at their core) not construction contracts; they are services agreements where the EPCM contractor typically takes responsibility for project design, manages procurement of contractors and suppliers, and coordinates their work through to completion. Unlike the EPC model, where the contractor instructs and has contractual recourse to subcontractors and suppliers, the EPCM contractor is not party to the various works or supply contracts. Instead, these agreements are entered into directly by the owner. EPCM contractors do not assume turnkey risk or act as the single point of responsibility. The owner assumes greater completion and financial risk if the project exceeds budget or is delivered late. Under an EPCM structure, liability for the works will be allocated throughout the various work packages to distinct contractors/suppliers; while design, management, and coordination risks rest with the EPCM contractor.
EPCM contracts are increasingly adopted in industries and/or for projects where EPC contractors are unwilling to assume significant risks or where owners seek greater control over project delivery – sometimes at a premium. Historically common in mining and oil & gas, EPCM contracts are now increasingly applied to a broader range of infrastructure and industrial projects.
EPCM structures may initially seem cost-effective for project owners, but cost savings often diminish during execution as owners encounter (i) greater in-house costs for contract management and coordination; (ii) potentially uncapped fees from the EPCM contractor; (iii) the cost of resolving programme delays; and (iv) the possible costs associated with managing multiple, concurrent disputes with the various counterparties. The risk of escalating costs increases when owners lack sufficient in-house resources or systems to manage on-site outcomes and coordinate multiple counterparties – each with varying levels of experience and capability.
We are seeing an increasing number of complex construction arbitrations arising out of EPCM structures.
In EPCM contract structures:
-
all parties should ensure contract documents, including technical specifications, adequately clarify the parameters of the interfacing works packages;
-
ensure the dispute resolution mechanisms across the project contract suite talk to each other and/or have all parties agree to a dispute resolution umbrella agreement; and
-
adopt arbitral rules with clear and well-worn consolidation and joinder provisions.
Our team has the relevant expertise to help businesses navigate this emerging area. Please contact us if you would like to explore this topic further in the context of your project or potential project.